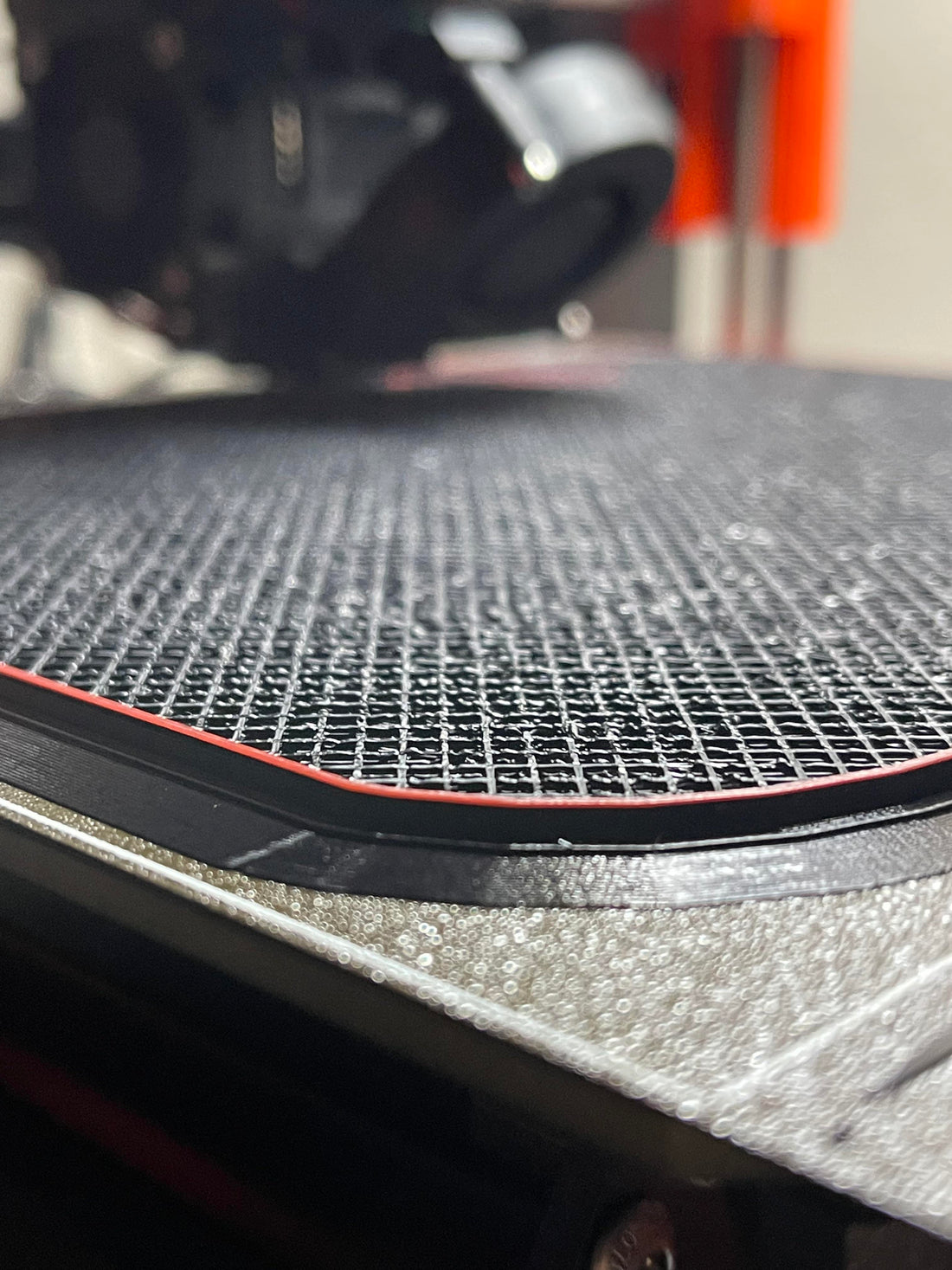
Grid Infill is Destroying your 3D Printer! - Here's what to use instead.
Share
What is Grid Infill?
Infill is the internal structure of a 3D print which makes the model partially hollow. This allows for considerably faster print times and great material savings while maintaining high strength. Grid infill refers to the the lattice structure of the infill which repeats throughout the entire height of the print.
Why is Grid Infill Commonly Used?
Many of the most popular 3D printing slicers such as Prusa Slicer or Bambu Studio use grid infill as the default settings, meaning the majority of users slice their prints with these settings. Furthermore grid infill has been consistently used for many years due to its simplicity and speed of printing in relation to the strength of the print on all axes.
So Why Should You Stop Using Grid Infill?
Despite all the positives that grid infill offers, it presents some major drawbacks that make it one of the most straining infill patterns to use for 3D printing:
Due to the nature of grid infill, the nozzle passes over areas where material as already been deposited. This effectively acts as a speed bump when printing at high speeds as the nozzle doesn't have enough time to melt the section it is passing over. This results in a clicking or scratching sound along with heavy rattling of the print head and vibrations throughout the whole machine.
On some 3D printers, this can cause extremely poor print quality as the vibrations cause ringing and poor surface quality throughout the print. Even if these severe issues don't show, the continuous motion of the nozzle hitting overlapping sections at high speeds will slowly wear on your 3D printers mechanics, thus wearing it out faster.
What are the Best Alternative Infill Patterns?
Gyroid
- Pros
- High strength to weight ratio.
- Equally strong on all axes.
- No overlaps when printing.
- Cons
- Longer print times due to complex structure.
- Many vibrations when printing with high infill percentage.
Honeycomb
- Pros
- High strength to weight ratio.
- No overlaps when printing.
- Allows some slight flexibility.
- Cons
- Stronger on the Z axis.
- Very high print times compared to other infills.
- High material usage.
Rectilinear
- Pros
- Fastest print speeds (Excluding lightning infill).
- No overlaps when printing.
- Good for high infill density.
- Cons
- Potential weakness at 90 degree corners.
- Lower strength to weight ratio.
- Not ideal for high detail models.
My Personal Choices
For lower infill prints at 5% to 30% infill, I recommend using gyroid infill as it has a high strength to weight ratio in all directions, while still being relatively quick to print with no overlaps.
For higher infill prints of 30% to 100%, I recommend using rectilinear infill as it is fast and efficient to print whilst minimising vibrations that arise when printing gyroid infill at higher densities.